3D Print 001 - SLS TPU
Conceptual Shoe studies utilizing custom algorithms in Grasshopper

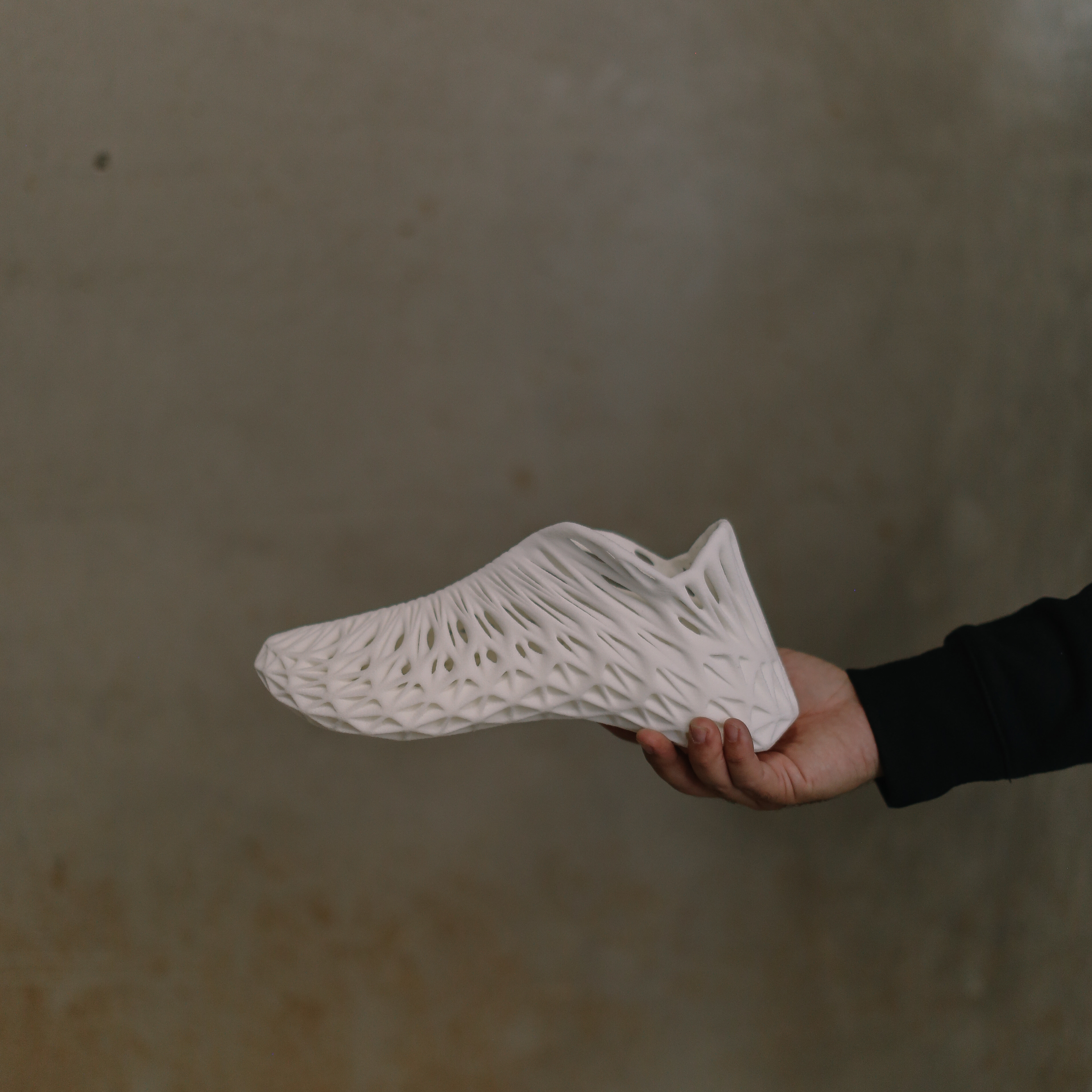
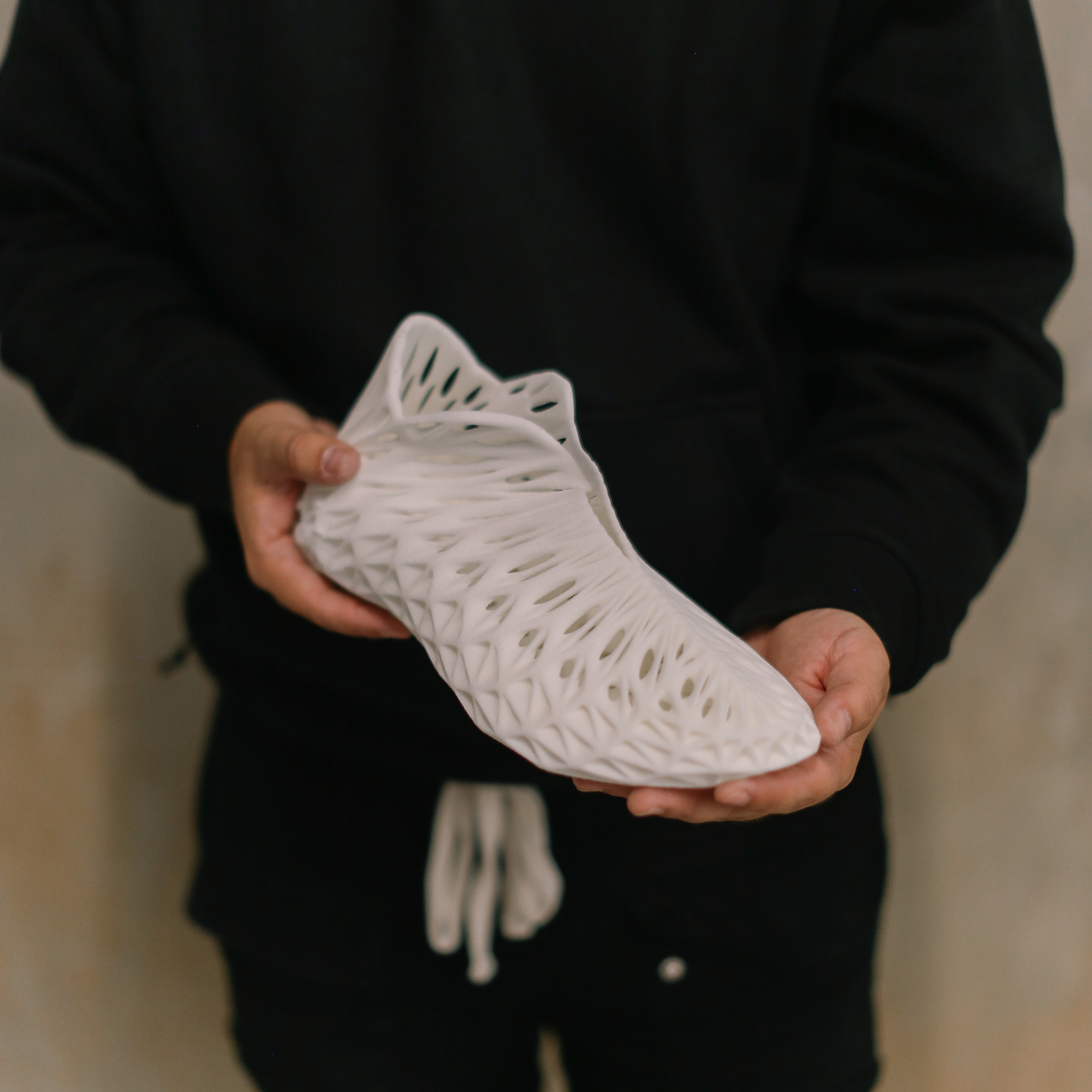
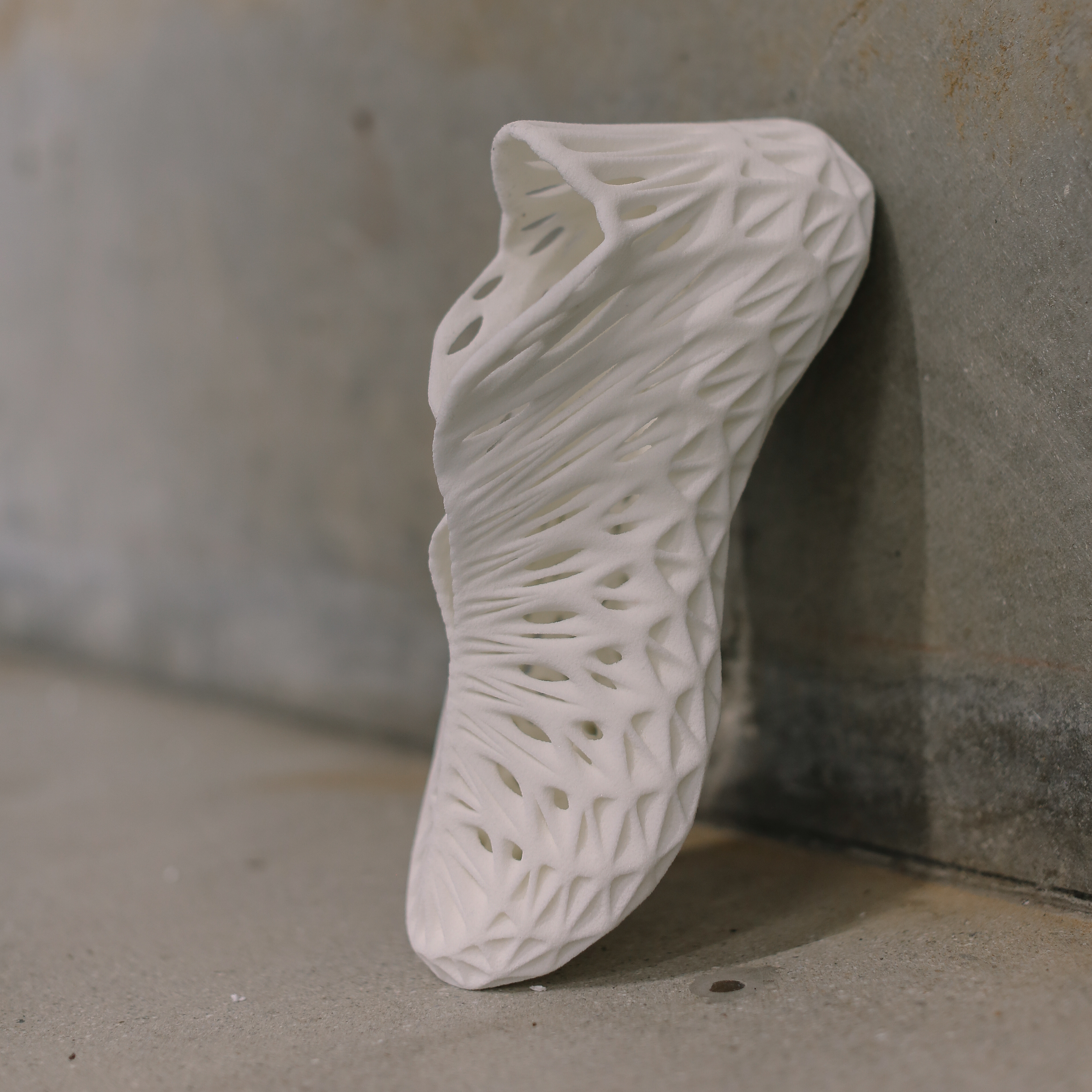
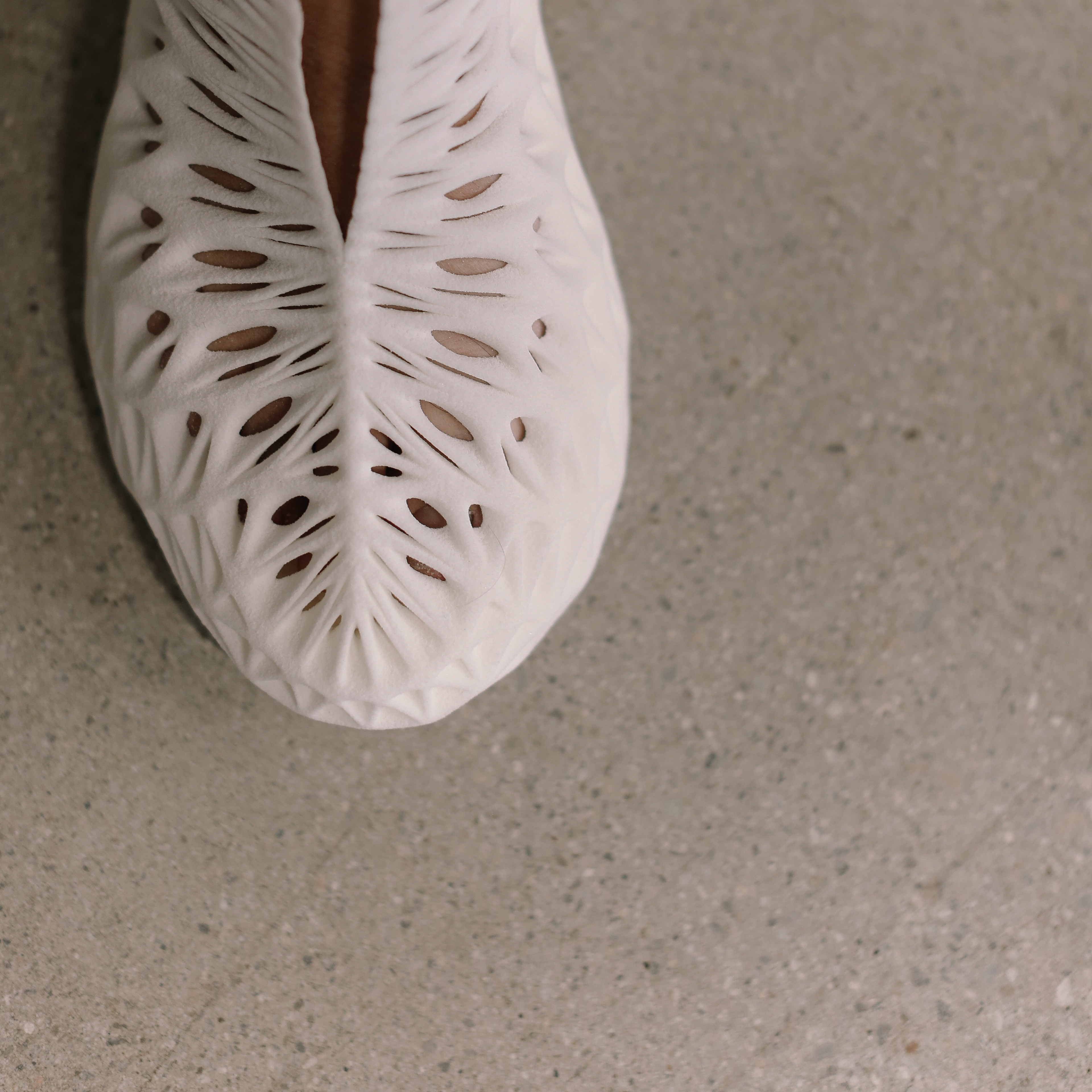
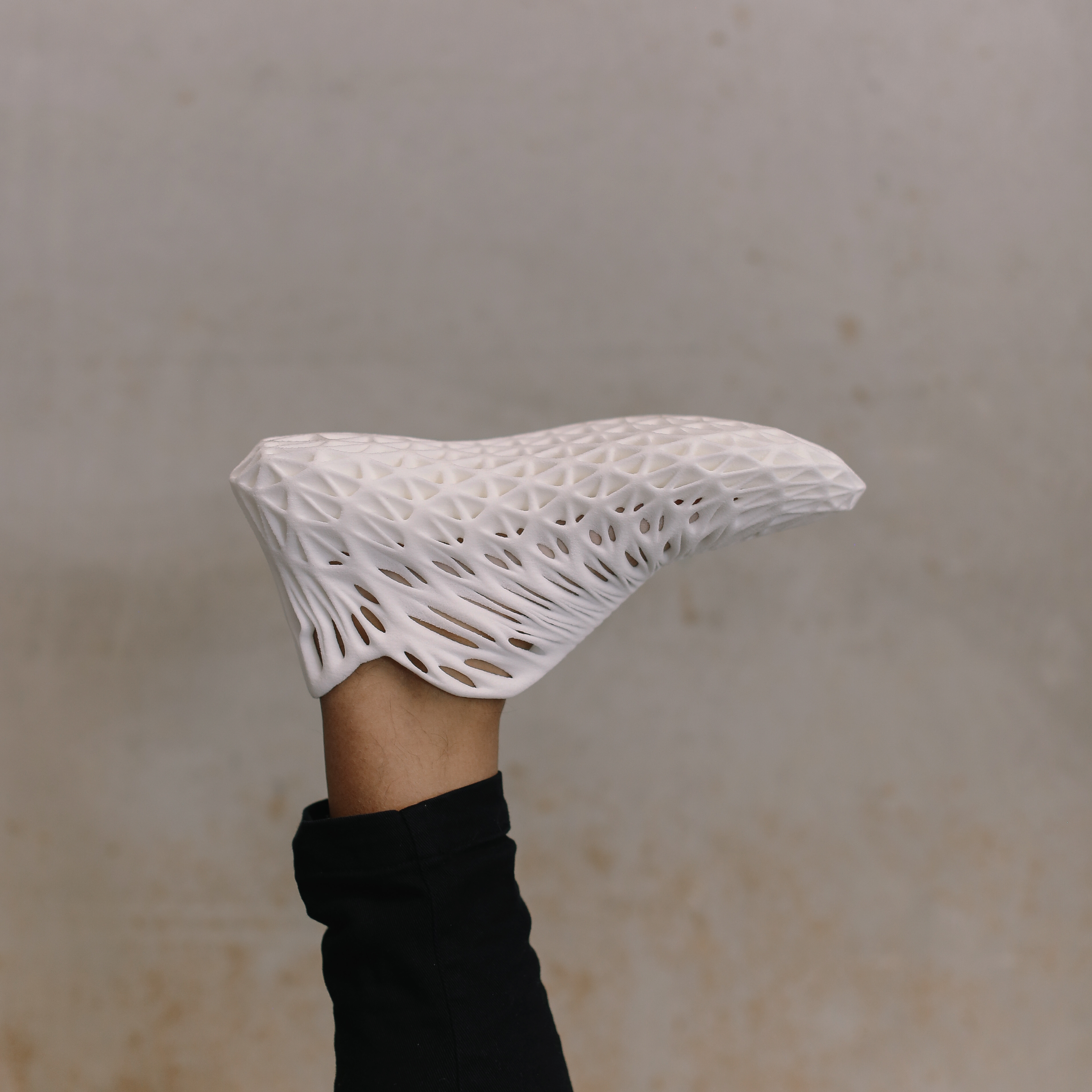
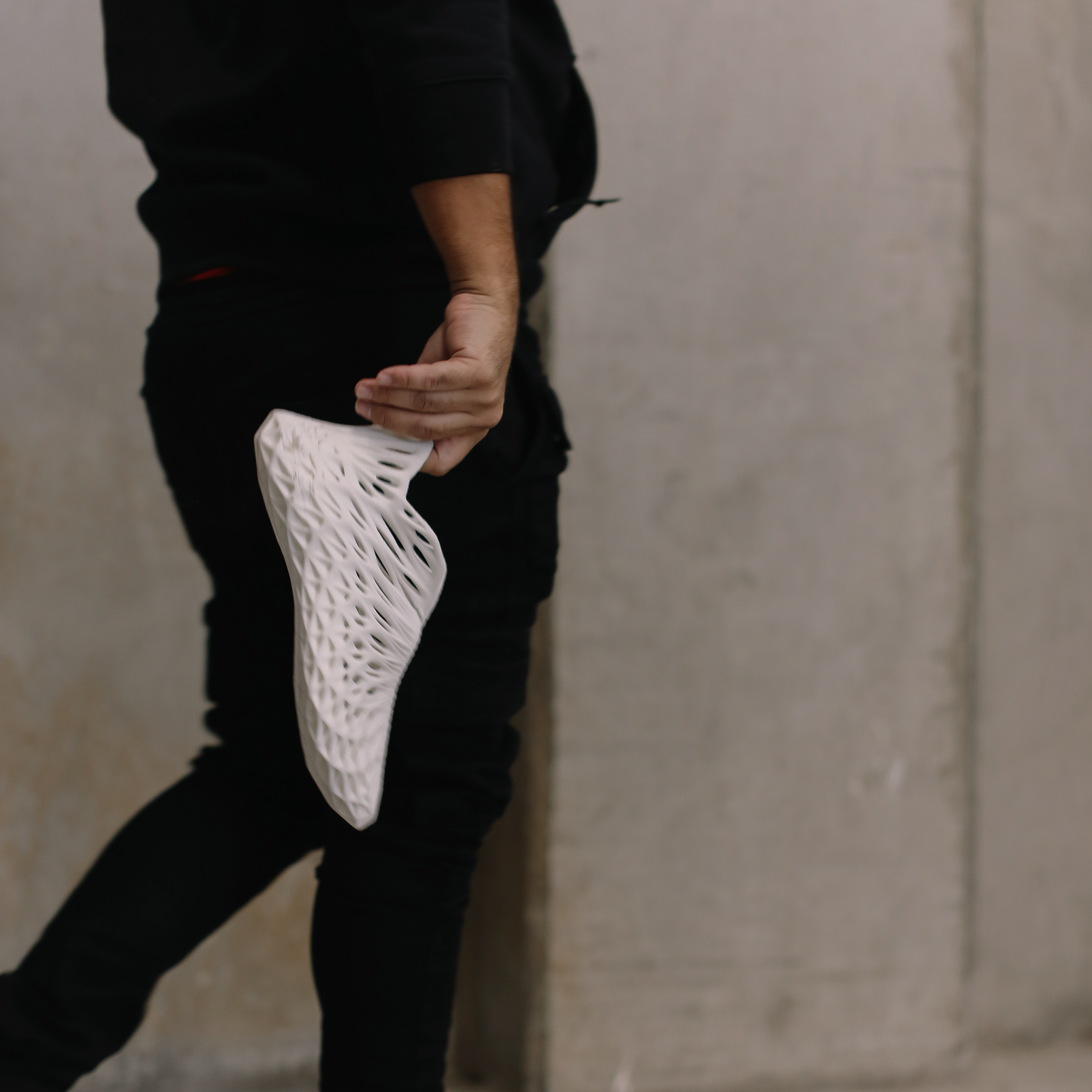
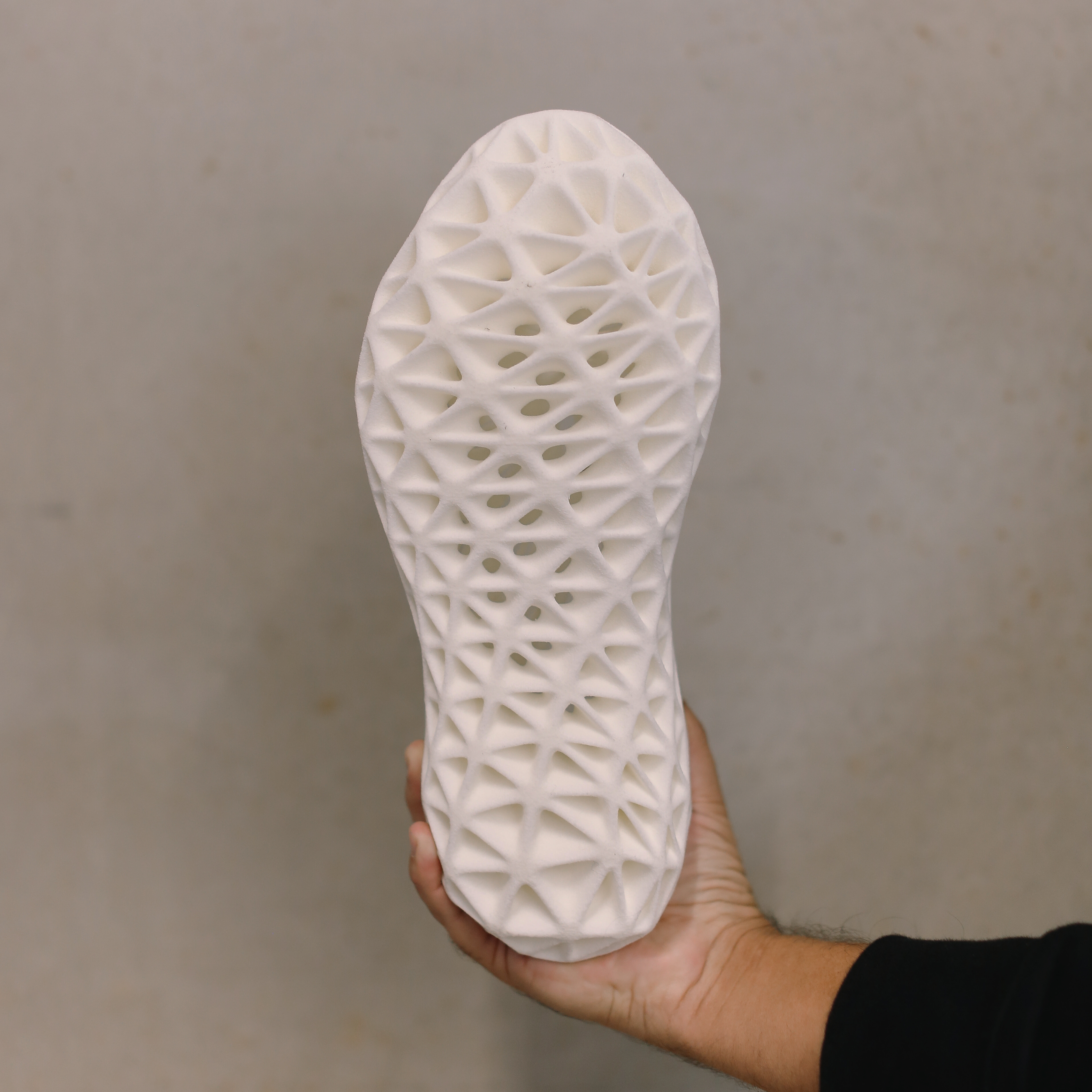
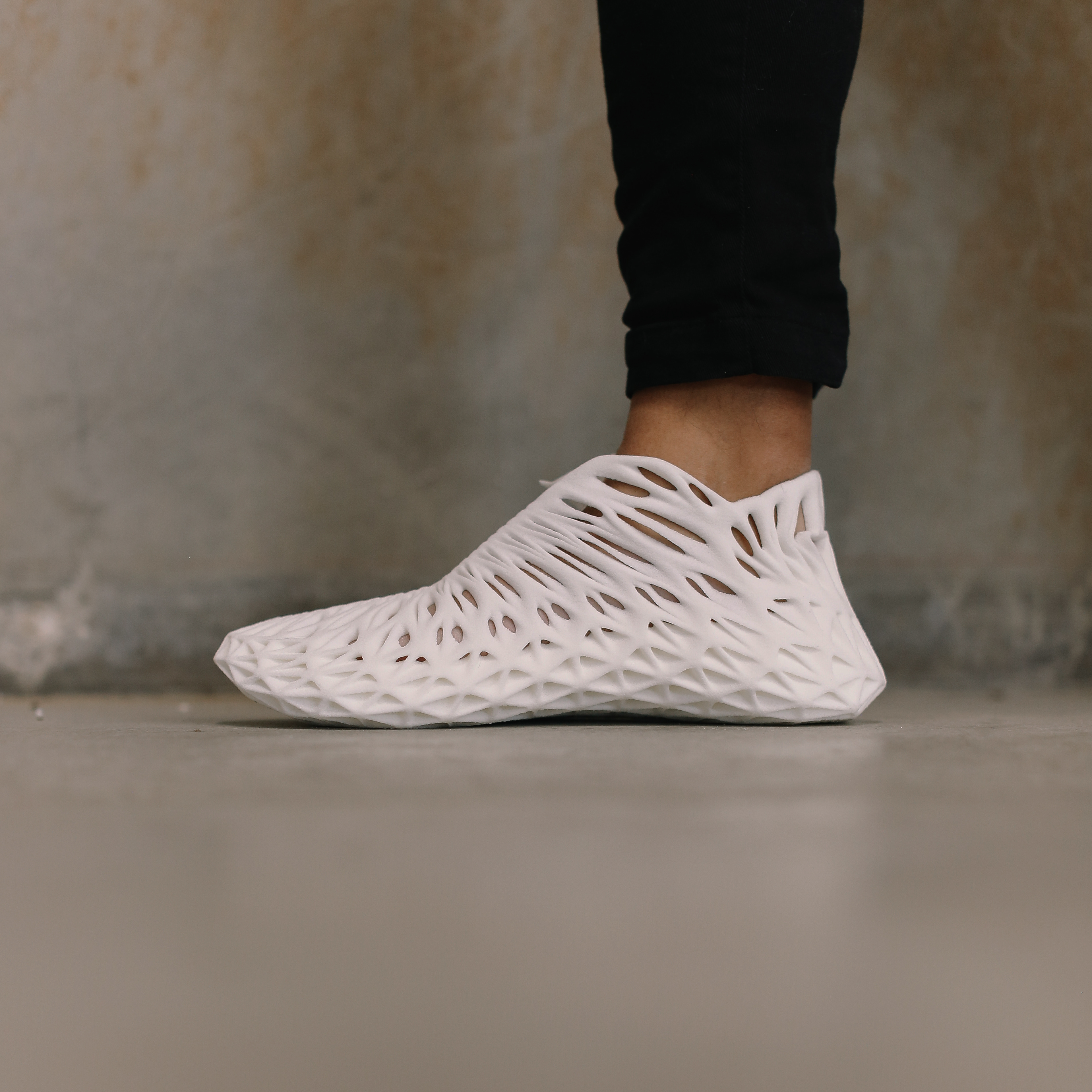
LEAD DESIGNER - PARAMETRIC DESIGN
AWARDS: Red Dot Award: Design Concept | Concept | Fashion and Accessories - Print 001XT
Print 001XT by Parametriks is a fully 3D printed parametric-based shoe, made using Selective Laser Sintering (SLS) which is a process that uses a high-power laser to sinter small particles of polymer powder (thermoplastic polyurethane (TPU) ) into a solid structure. Based off of a interwoven mesh structure that flips between rectilinear and diagrid based forms, this laceless trainer blends the function of a lower and upper, an insole and an outsole as well as the aesthetics and function of a traditional shoe into a singular form.
This initial concept design was printed using Selective Laser Sintering (SLS) which is a process that uses a high-power laser to sinter small particles of polymer powder into a solid structure. This method is a low-cost solution used for initial testing and prototyping. The polymer used is thermoplastic polyurethane (TPU) which provides elasticity while still maintaining a high degree of detail and structure per the original designed form. Post processing on the material will be studied in order to change grip and sheen.
This is the next generation of shoe design. Not based on a homogeneous model that fits most, this design reacts directly to user input based on foot shape, needed ergonomic cushioning and can be tuned based on use type (leisure to advanced sport). Not only does this provide a bespoke solution for the wearer but means a single design can span across different typologies based on the complexity of the base model.
In 2008, a leather shoe was found in Armenia from 3500 BC which closely resembles the shoes we wear today, with one big difference: the shoe was comprised of a single piece of leather which wrapped the top and bottom of the foot. In a similar manor, these 3D printed shoes are based on a singular continuous last surface gathered from a foot scan. An additional continuous surface is offset from the last to create the overall exterior shoe form. Based on a mixture of aesthetic shape choice (subjective) and ideal cushion (objective), the offset distance varies along the initial surface. Both surfaces are then divided into identical parallel meshes. A volumetric mesh of X and T profiles bridges the vertices to the face center between the two mesh faces. The result is a complex exterior form and perfectly fitting interior.
With a parametric-based model, the role of the designer changes from subjective/objective choice of the singular to curation of a multiplicity. The designer no longer designs a one-off, but an entire system which can then create a varied set of options that can be ranked and sorted according to performative aspects. All based on a singular flexible last mesh and it’s offset counterpart, various volumetric connecting grids can be created in order to completely change the aesthetic and performance of the particular shoe.
Shoes have been traditionally comprised of 2 main components: a sole and an upper. To some degree, this had made sense: the sole provided protection and cushion to the bottom of the foot while the upper provided light-protection to the top of the foot. With the advancement of 3D printing, this traditional model is being challenged. By pairing 3D printing with a parametric-based model, the design of the shoe can be modified to respond to various inputs. When both of these are paired with an accurate foot scan and foot pressure mapping, a bespoke shoe can be created per the user.
Print 001XL is a single print made of a single material, meaning no glues or attachments that break down over time and cause the separation between sole and upper. These shoes are printed-to order which reduces over-production and decreases the amount of products that end up in landfills. They are printed custom to the user, modified to foot shape and tuned to actual use.